Research direction
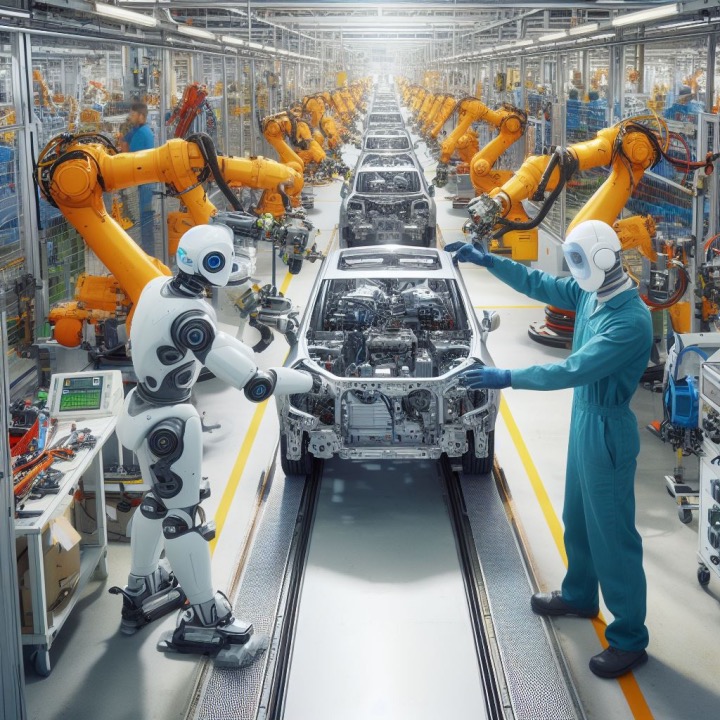
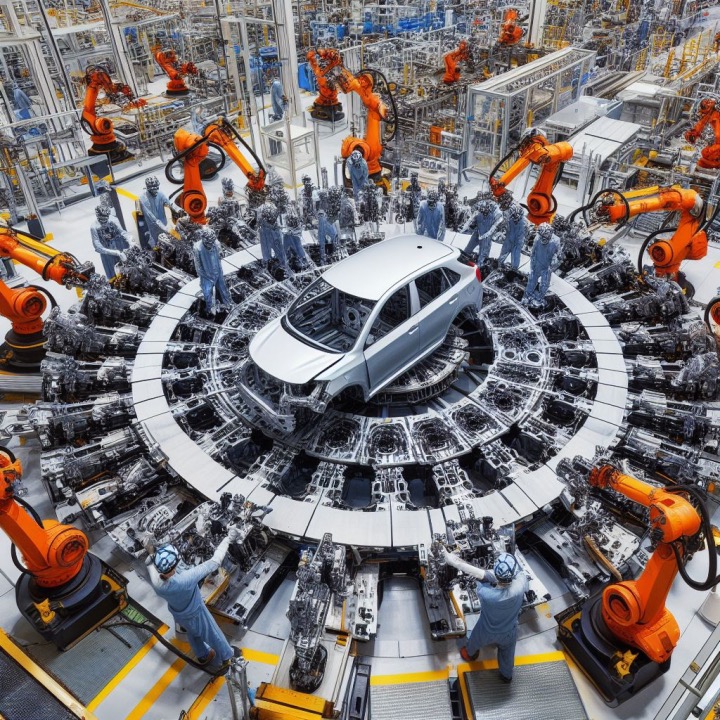
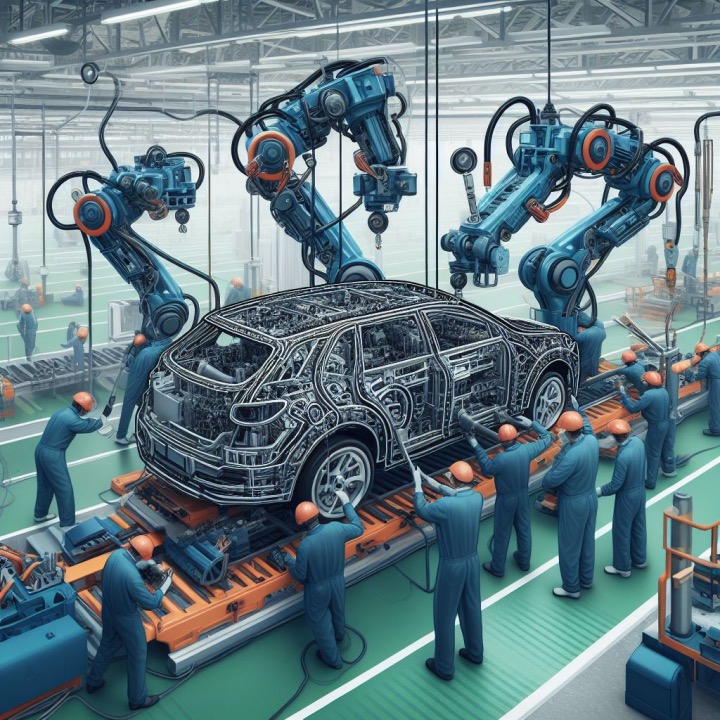
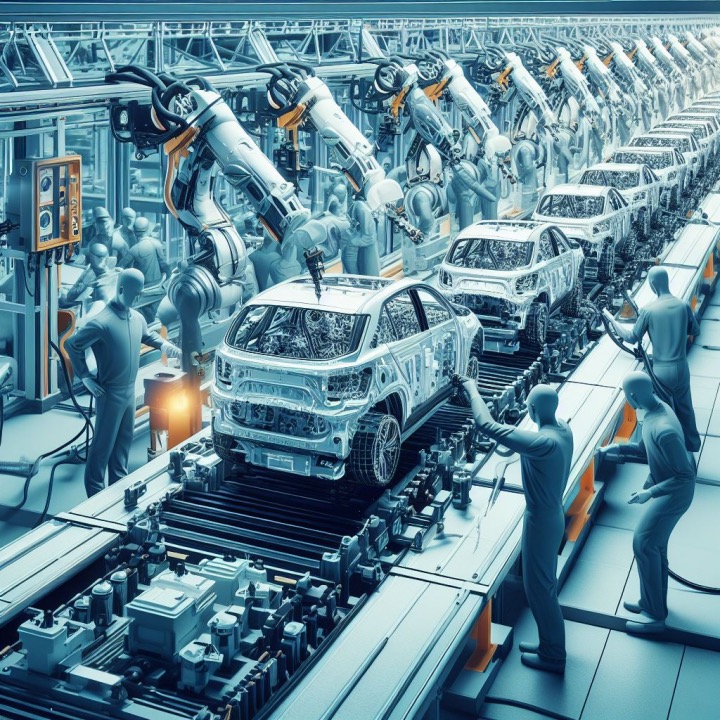
1. Optimization of Intelligent Dismantling Line Systems
Promote the full lifecycle management of products, enhance the resource utilization rate of industrial waste from the source, and support the construction of zero-waste factories.
Straight/U-shaped Dismantling Line: Utilizing modular workstation design and dynamic rhythm control technology to achieve rapid disassembly and classified recycling of standardized products such as home appliances and electronic devices.
Parallel/Bilateral Dismantling Line: Develop a multi-robot vision positioning system to break through the technical bottleneck of collaborative separation of heterogeneous components in large-scale equipment such as automobiles and machine tools.
Circular Dismantling Line: Innovatively develop an integrated system of circular tracks and intelligent sorting devices to establish a closed loop for the non-destructive recycling of batteries and precious metal components.
2. Distributed Manufacturing Network
Help manufacturing enterprises build a new type of production network with “centralized control + distributed execution,” significantly enhancing the resilience to supply chain disruptions.
Intelligent Order Decomposition Engine: Utilizing deep learning to predict regional production capacity loads and automatically generating the optimal distributed production plan.
Intelligent Order Decomposition Engine: Predict regional production capacity loads through deep learning and automatically generate the optimal distributed production plan.
- Virtual Factory Networking Technology: Supports dynamic reconfiguration of production units on demand, achieving “cloud access – intelligent matching – elastic invocation” of equipment resources.
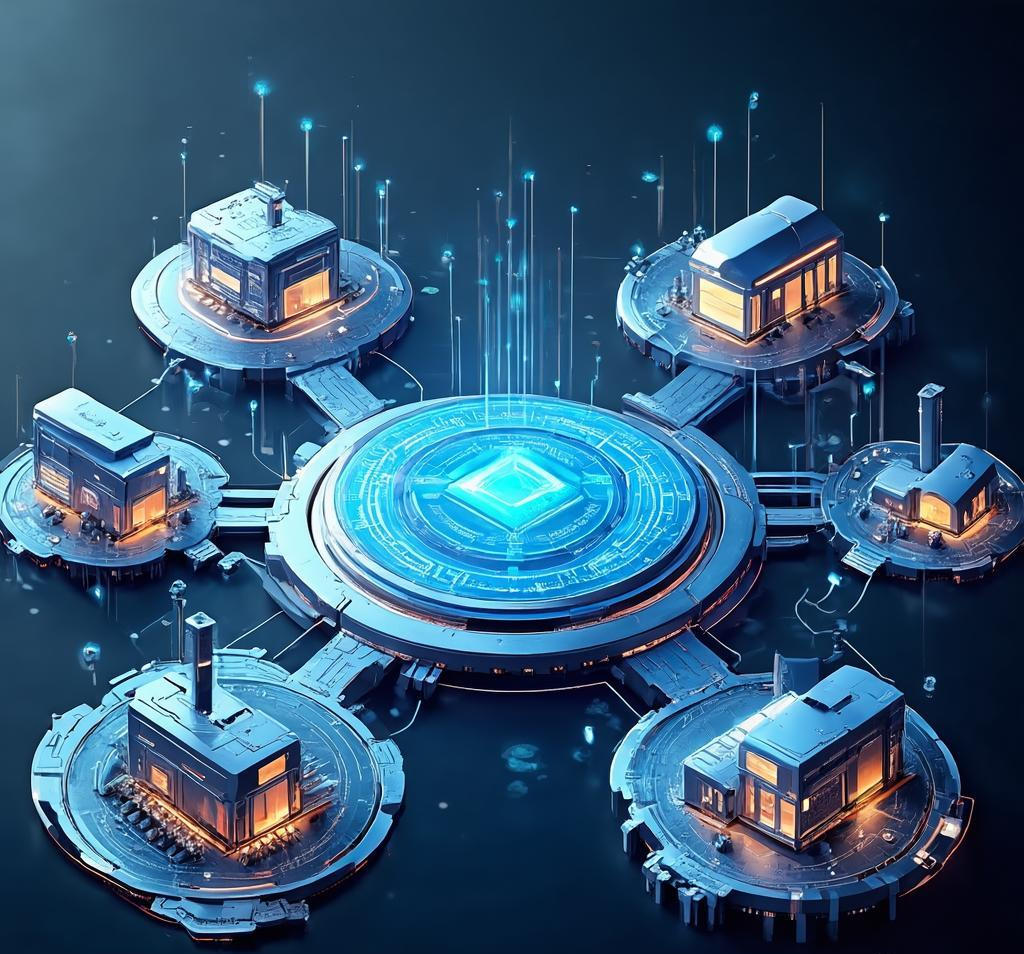
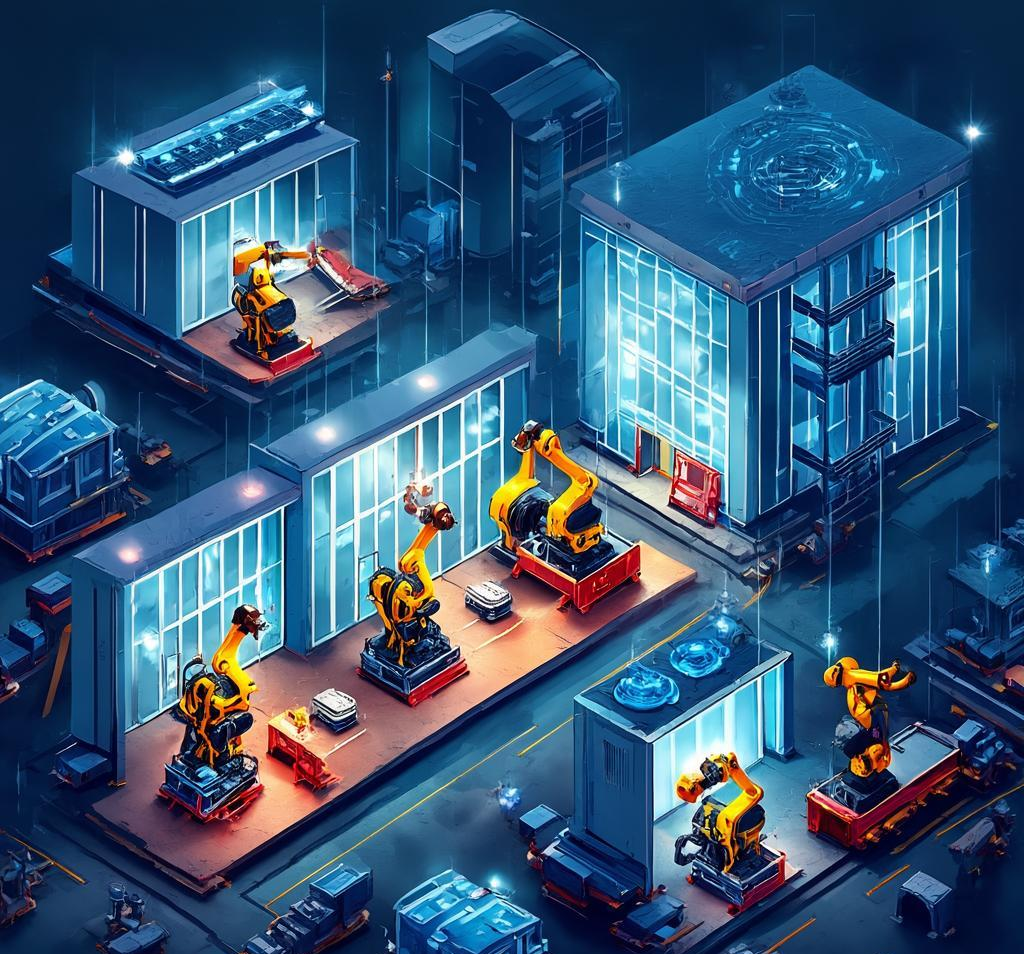
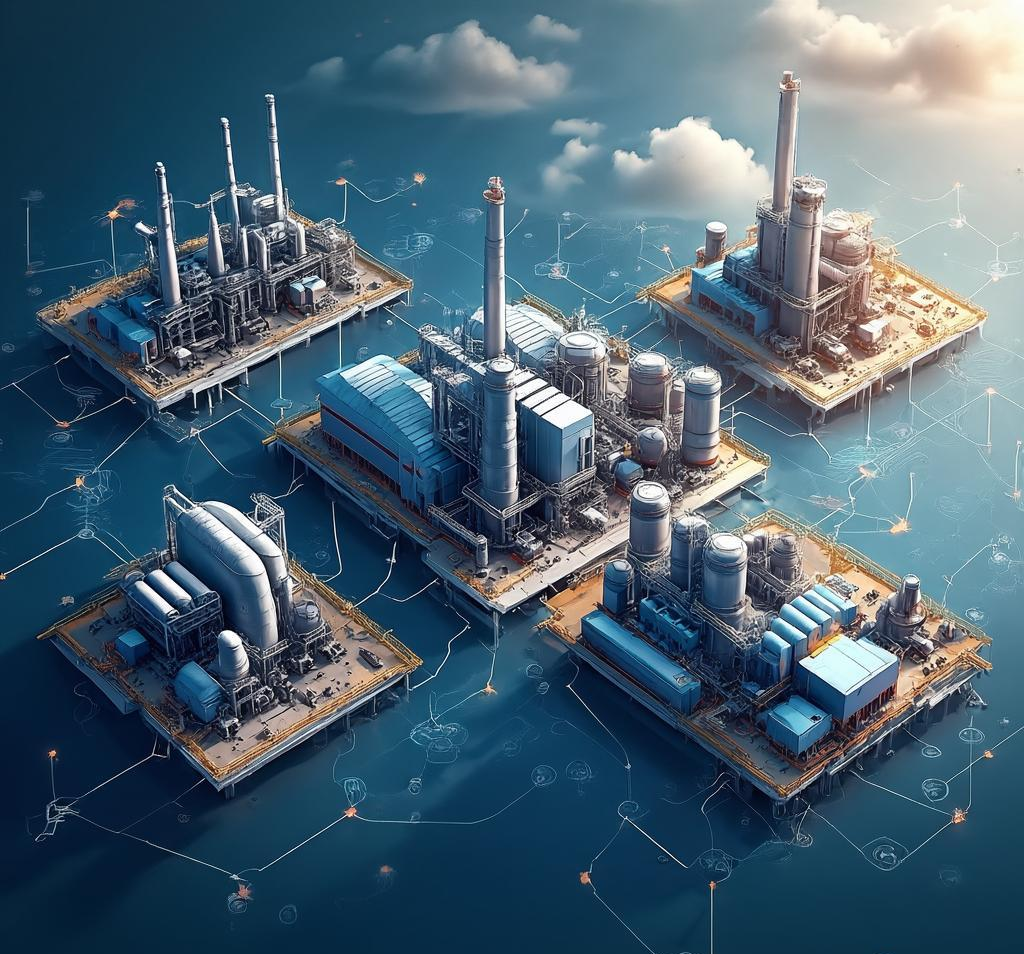
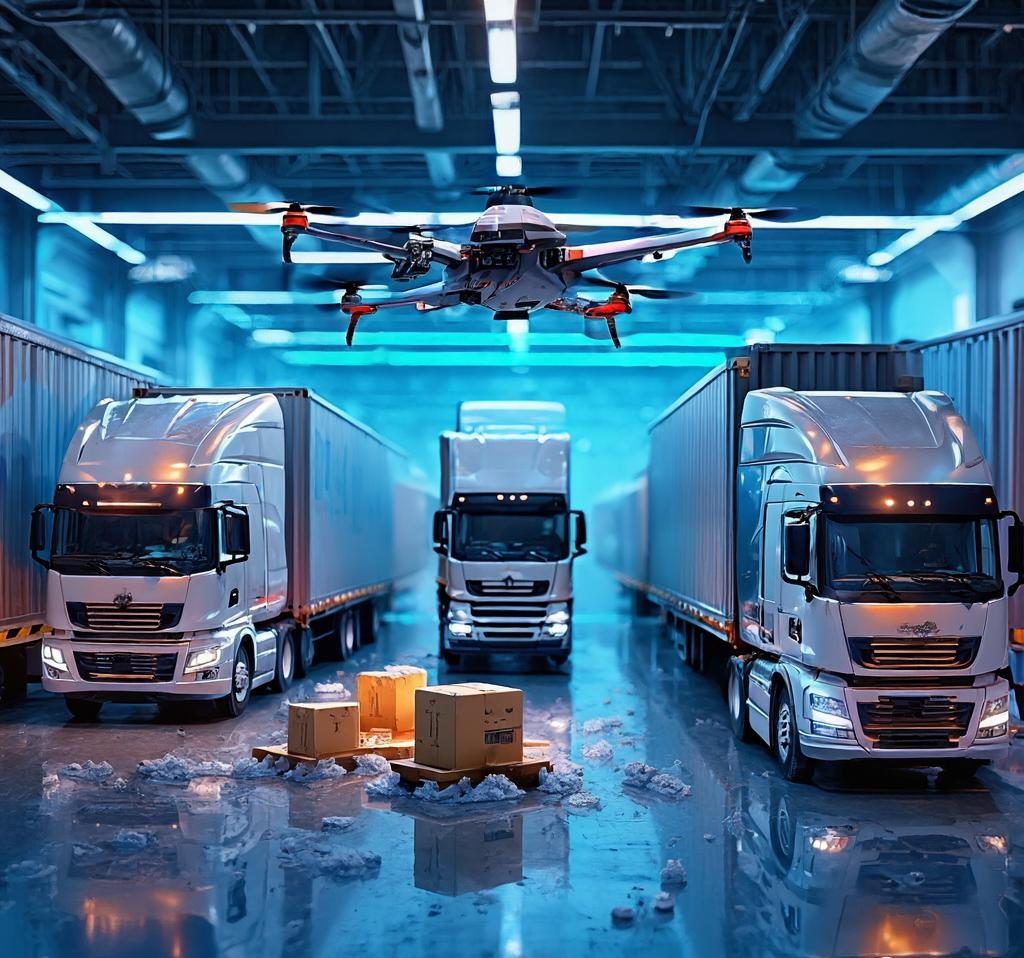
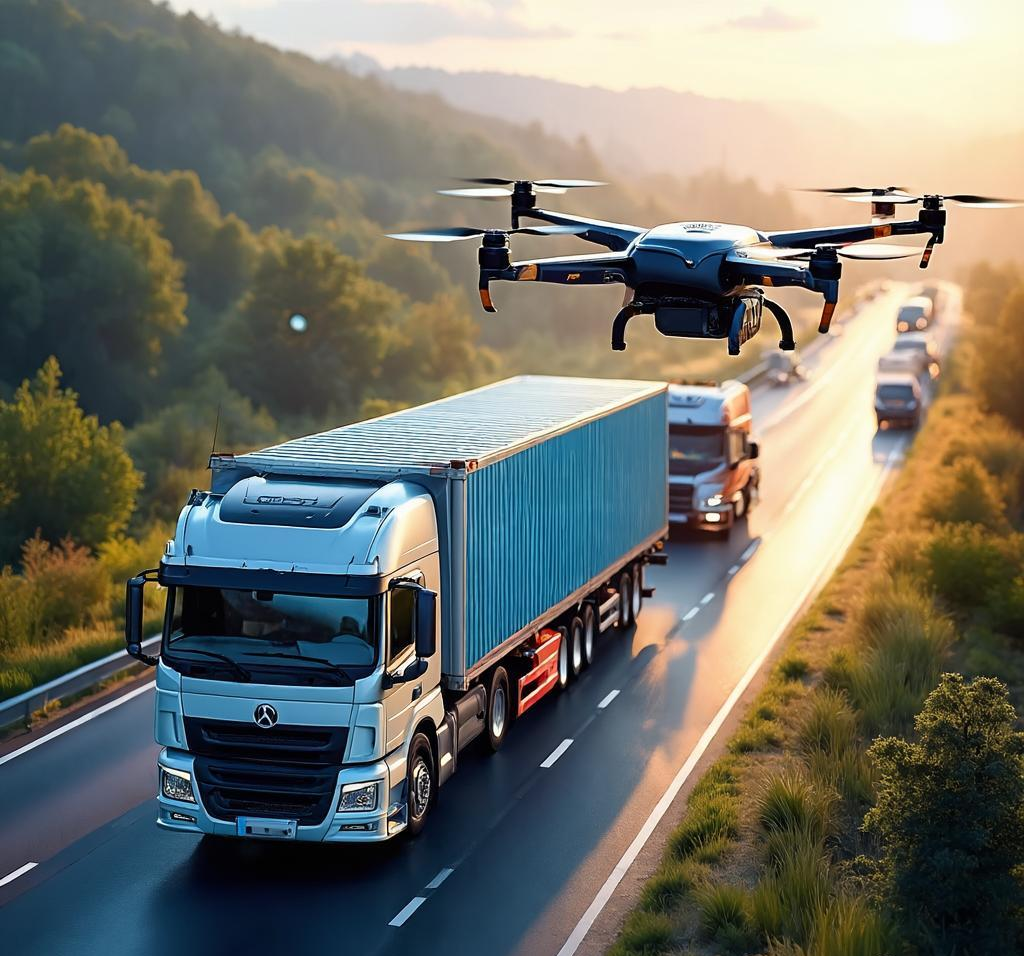
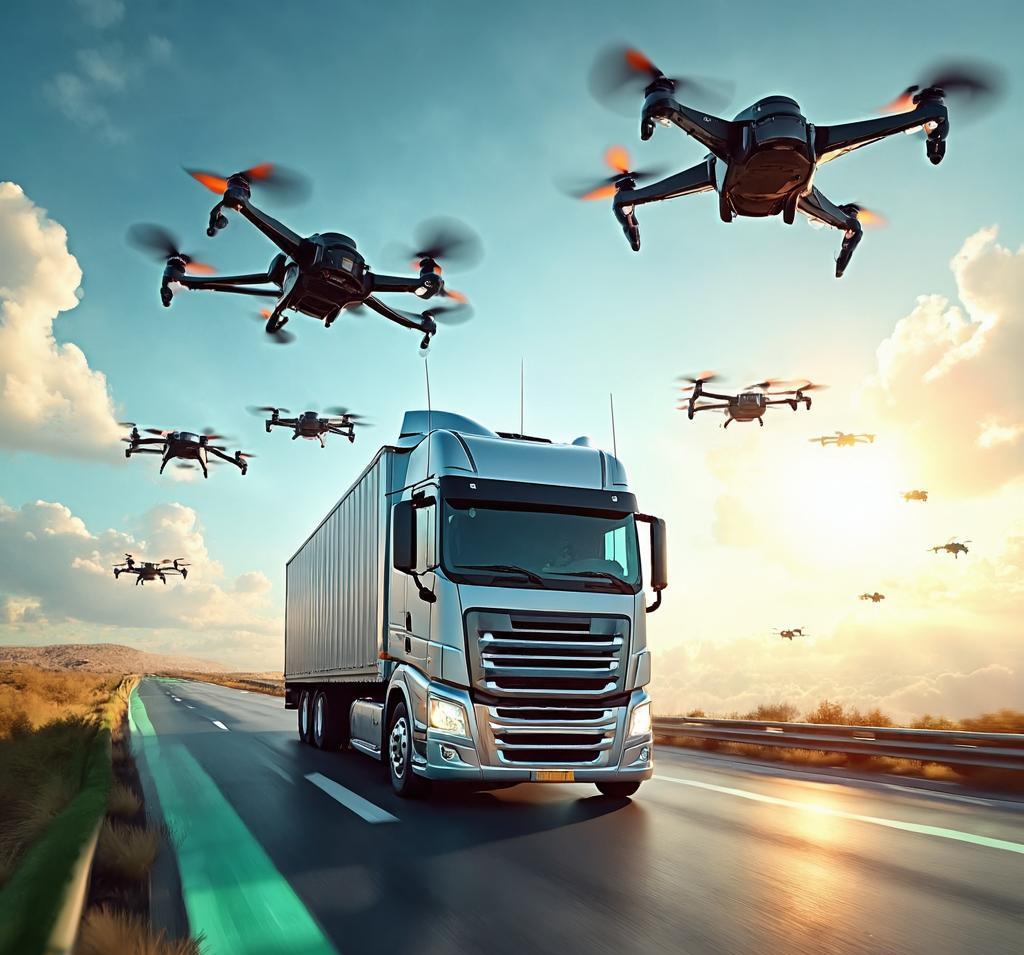
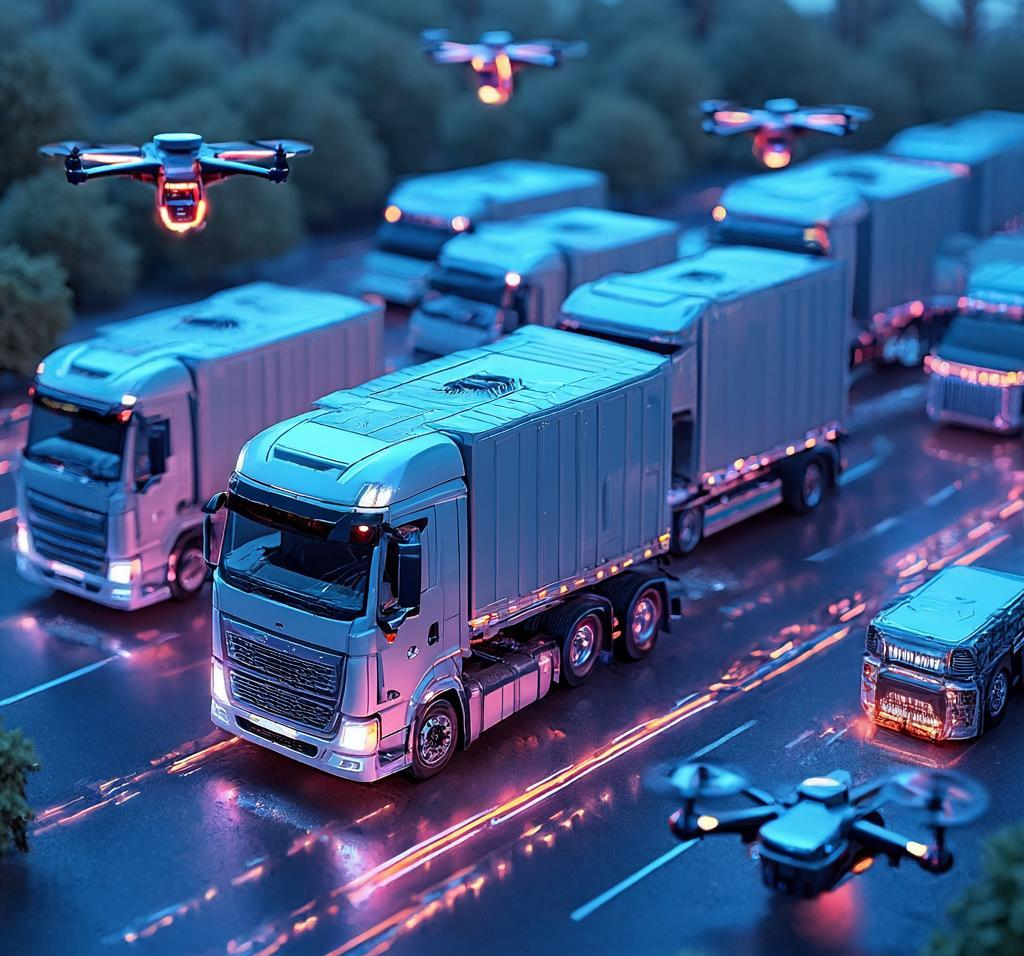
3. Intelligent Logistics and Distribution System
By constructing a logistics network that is “spatially three-dimensional and service-oriented with precision,” reliable solutions are provided for time-sensitive fields such as medical emergencies and fresh food cold chains.
Truck and Drone 3D Networking: Develop a heterogeneous carrier communication relay system to establish a collaborative mechanism between ground trunk transportation and low-altitude instant replenishment.
- Intelligent Loading Optimization Algorithm: Automatically plan the loading schemes for truck compartments and drone bays based on cargo attributes, enhancing the compatibility of product categories in a single delivery.
- Environmental Adaptation System: Integrates meteorological perception, dynamic obstacle avoidance, and endurance self-inspection functions to ensure the stability of delivery in complex scenarios such as mountainous areas and urban dense zones.
4. Quantum Intelligent Computing
Offer the potential for exponential acceleration in solving industrial optimization problems with a scale of hundreds of millions of variables.
Quantum Annealing Algorithm: Develop quantum-accelerated solvers for combinatorial optimization problems such as workshop scheduling and logistics routing.
Quantum Machine Learning Framework: Develop equipment failure prediction models based on quantum neural networks.
- Quantum-Classical Hybrid Architecture: Build a quantum-encrypted communication system that supports distributed manufacturing.
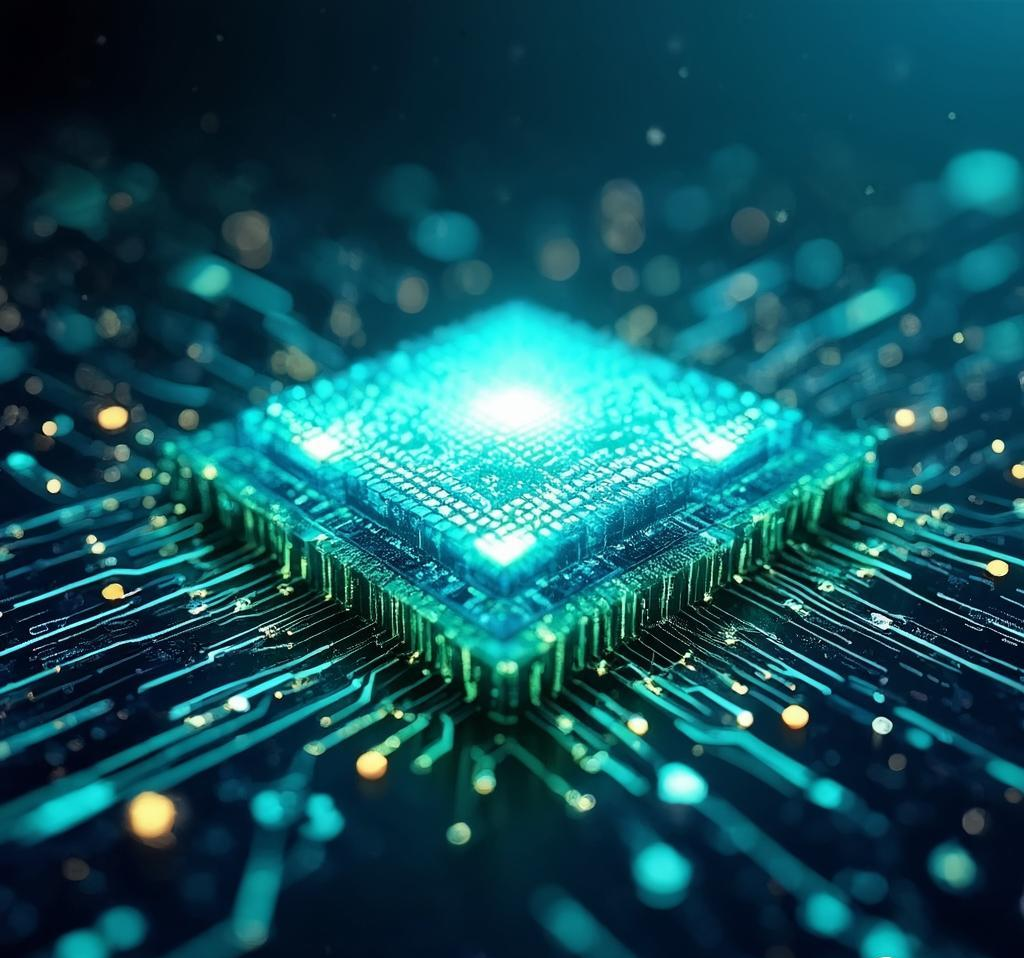
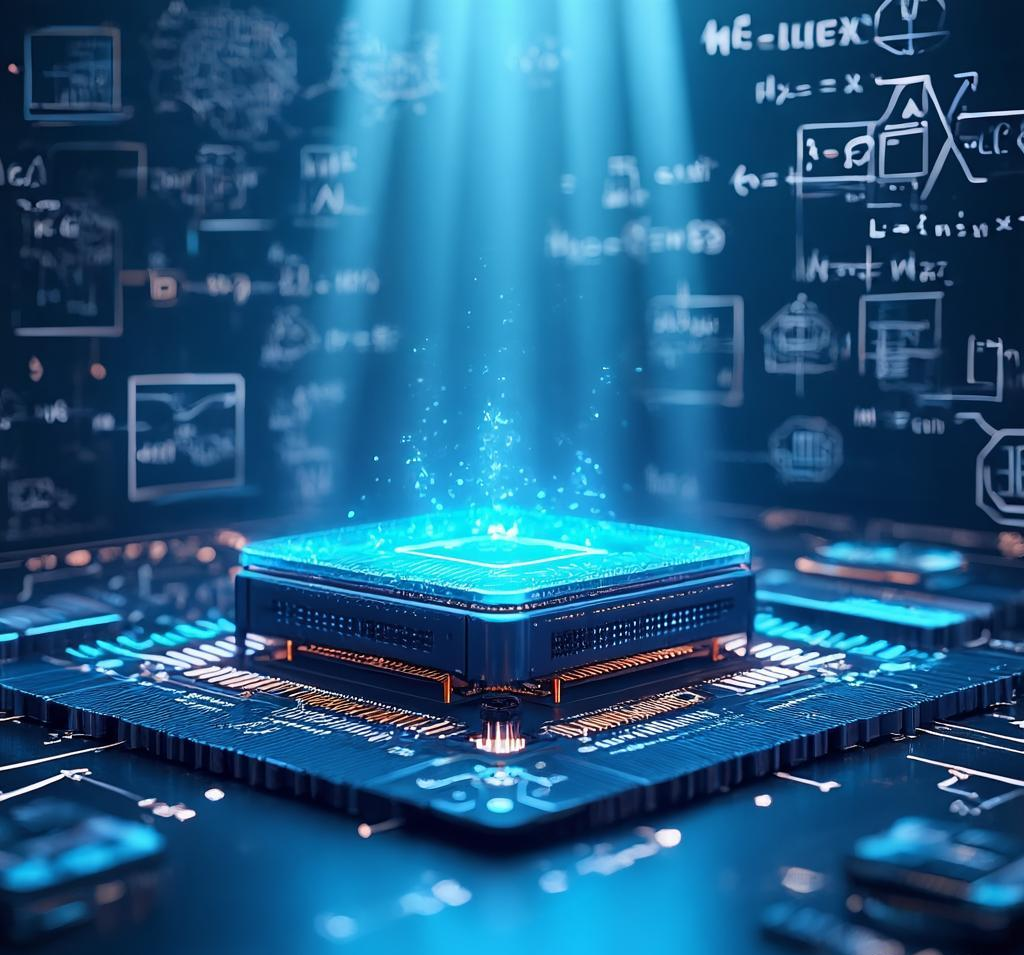
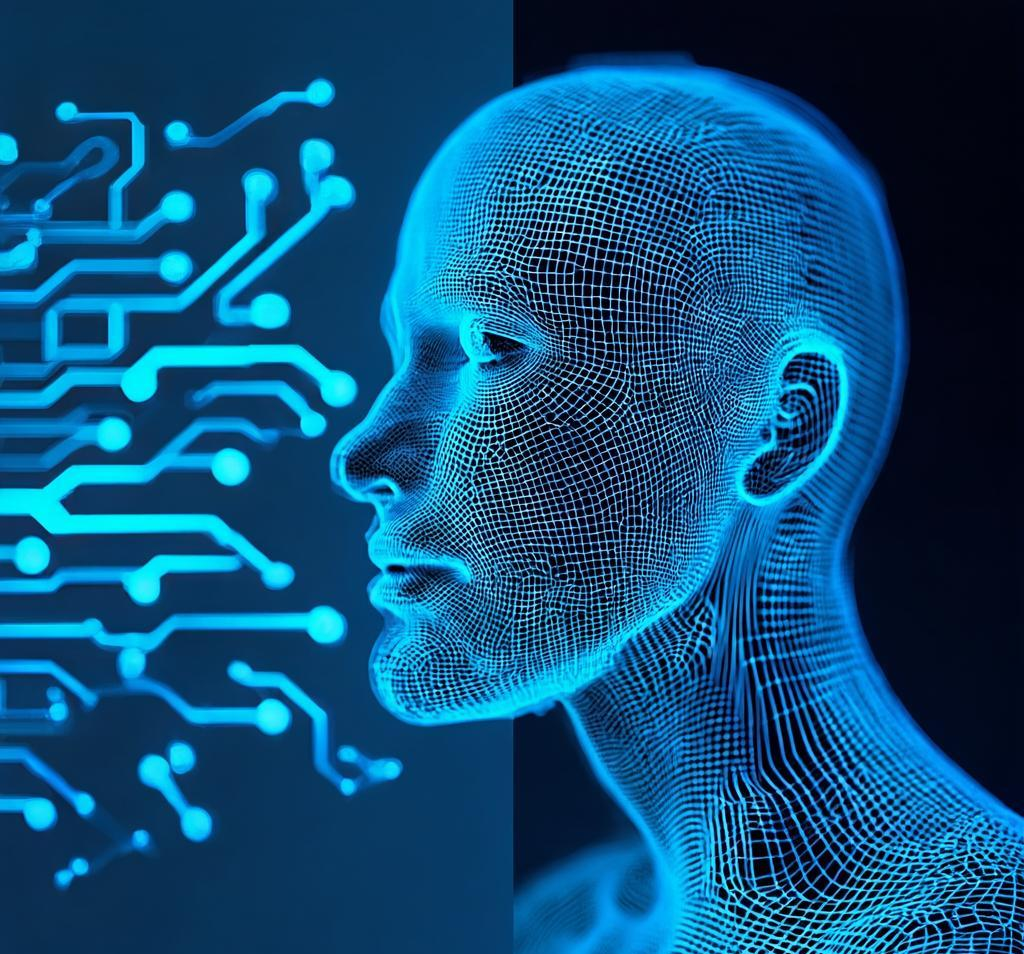
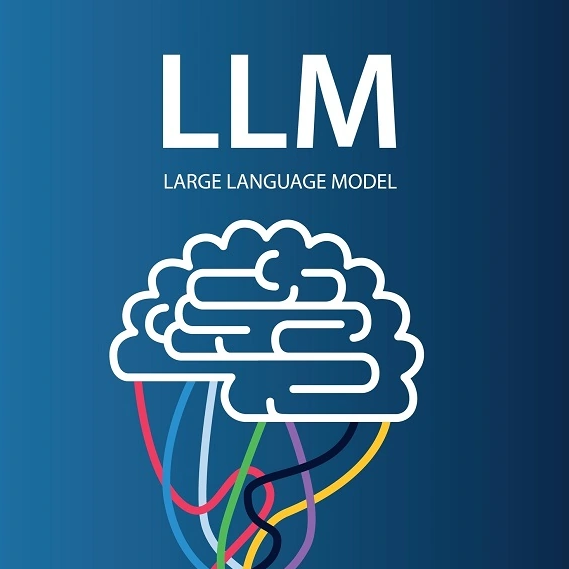
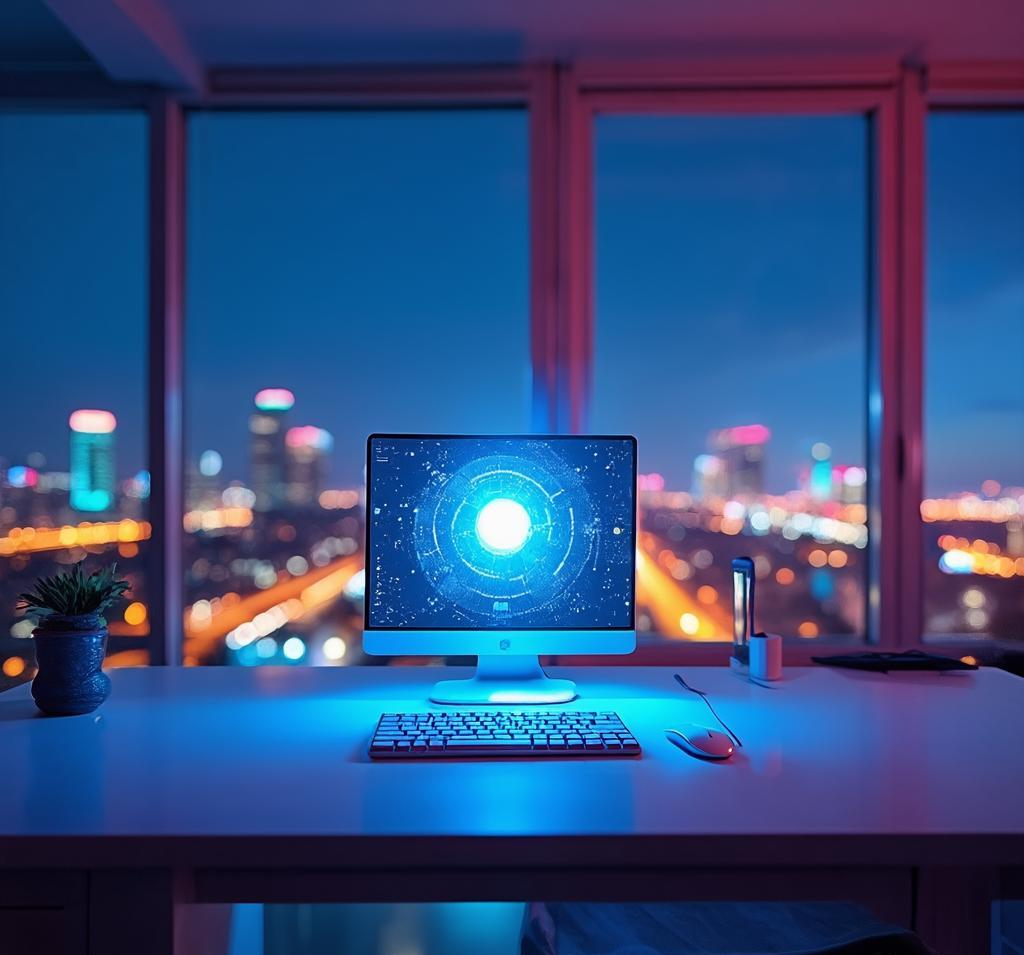
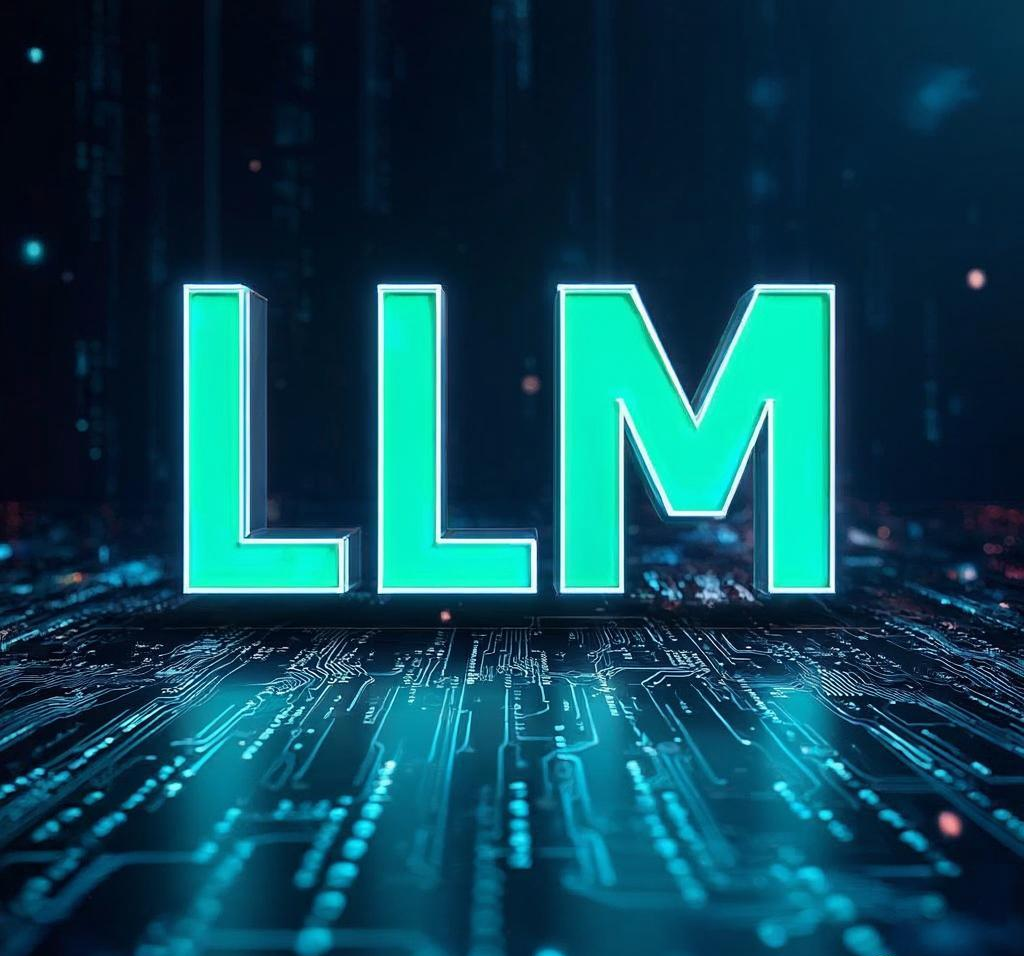
5. Industrial Large Language Model
Promote the transformation of the manufacturing industry from “experience-driven” to “knowledge-driven.”
Multimodal Industrial Knowledge Base: Integrates unstructured data such as equipment manuals, process drawings, and maintenance records.
Domain-Adaptive Training Framework: Develop fine-tuning techniques enhanced by manufacturing terminology and constrained by physical laws.
- Intelligent Decision Support System: Achieve semantic-level reasoning in scenarios such as production anomaly diagnosis and process parameter recommendation.
6. Online Real-time Scheduling System
Integrate rolling horizon algorithms to optimize scheduling strategies in real-time, achieving efficient, intelligent, and risk-resistant real-time decision-making and dynamic adjustments.
Streaming Data Processing Engine: Achieve second-level perception of sudden events such as order fluctuations and equipment anomalies.
Rolling Horizon Optimization Algorithm: Build a dynamic correction mechanism for adaptive scheduling strategies.
- Digital Twin Simulation Sandbox: Support multi-dimensional pre-enactment and risk assessment of scheduling plans.
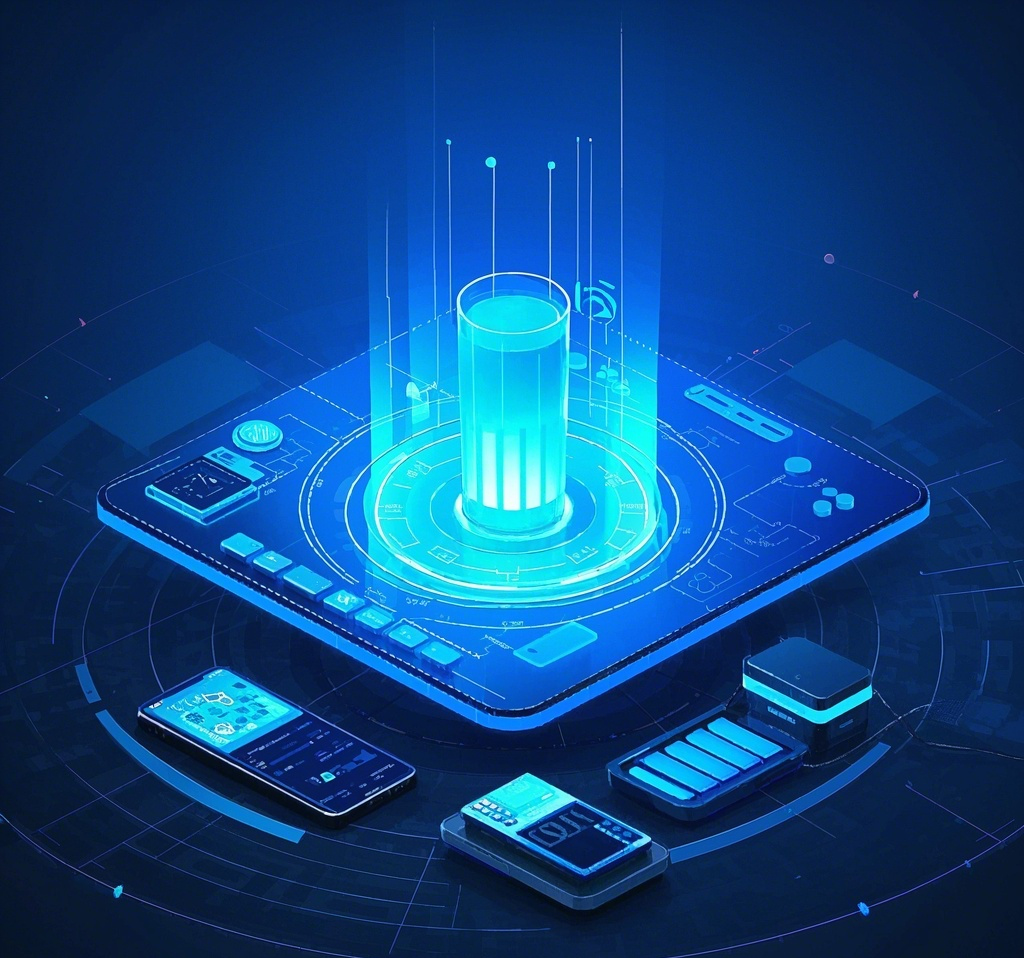
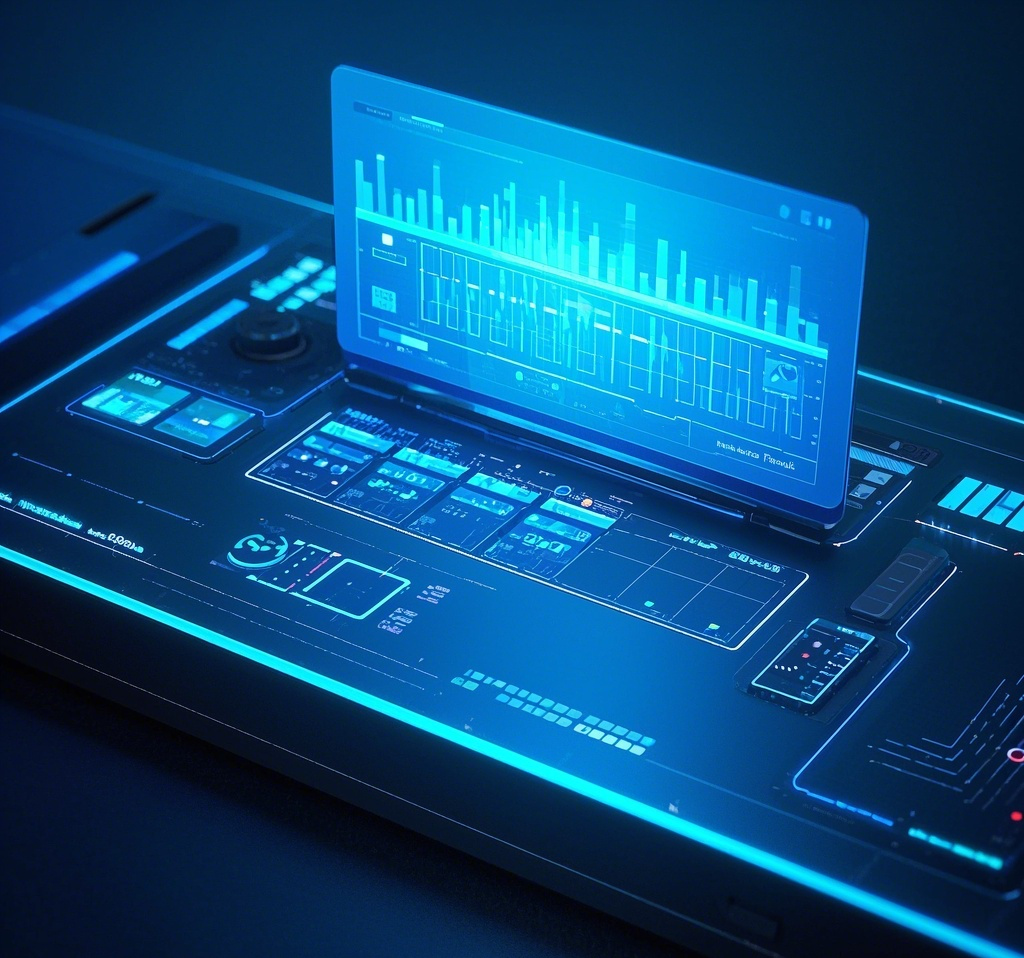
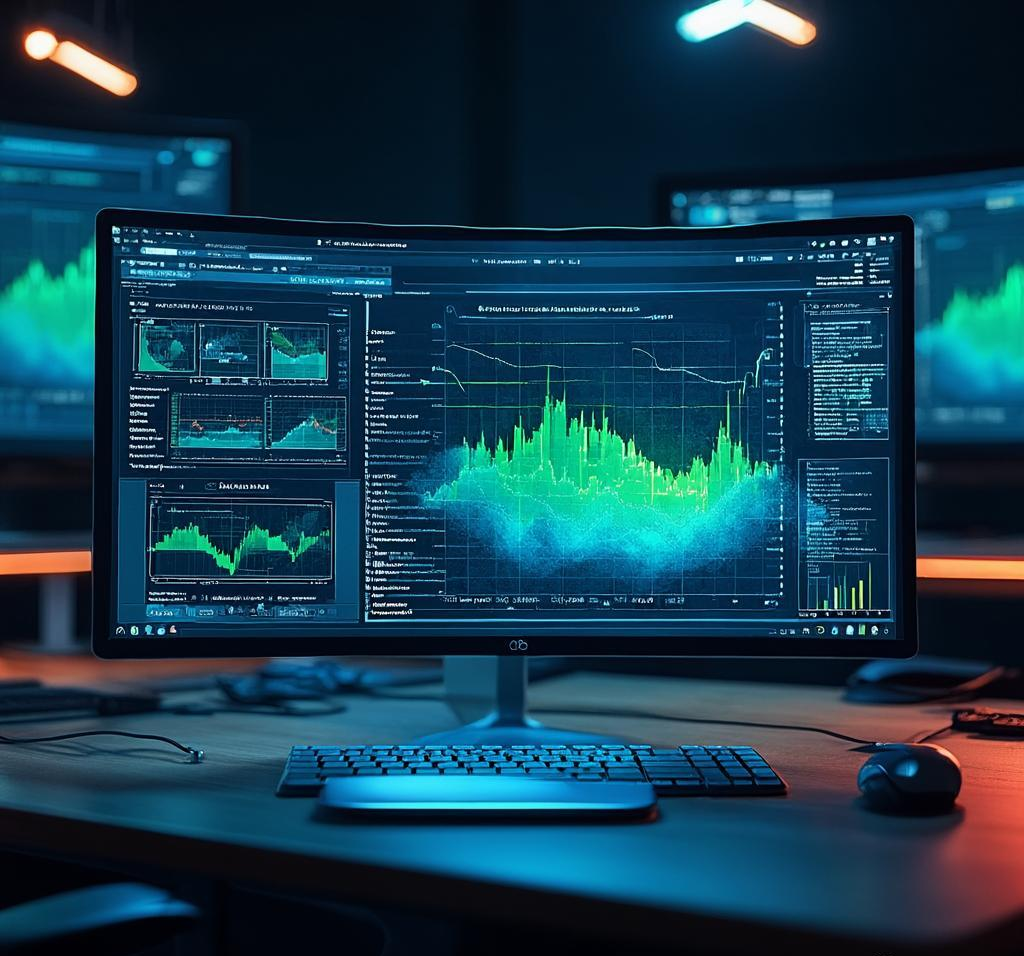
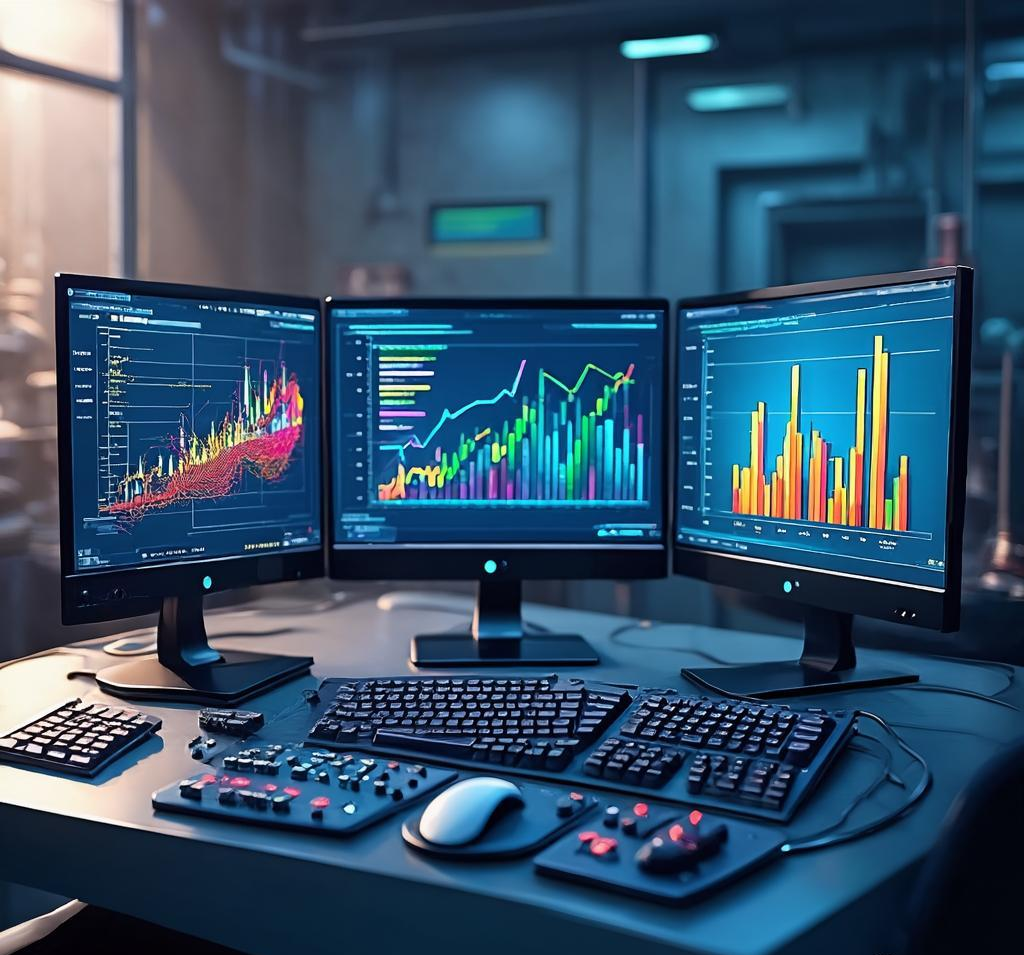
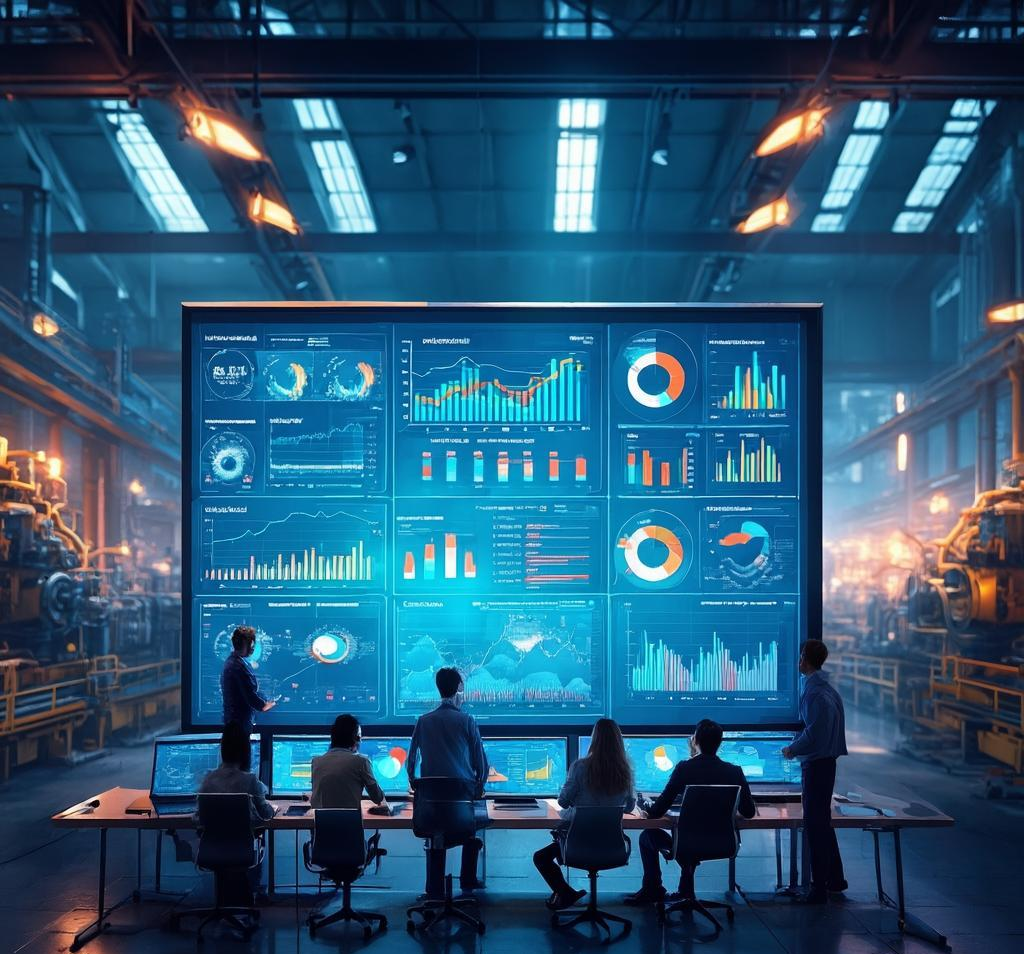
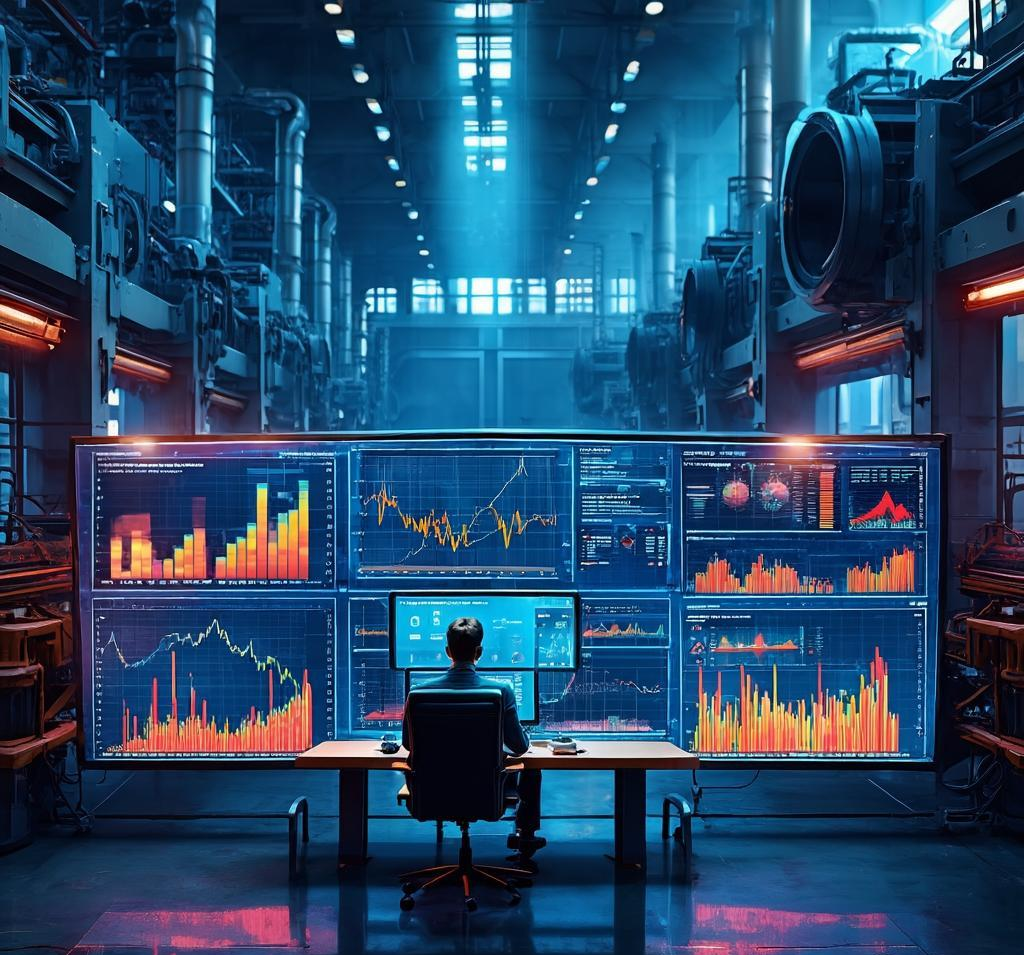
7. Big Data Analytics
Break through the conversion chain from “data – information – decision” to increase the proportion of data-driven decision-making in manufacturing systems.
Multi-source Heterogeneous Data Governance: Develop an industrial data lake architecture to achieve standardized cleaning and integration of data from equipment sensors, production logs, and supply chain.
Real-time Streaming Analysis Engine: Develop a time-series data analysis framework that collaborates between edge computing nodes and cloud computing power, supporting millisecond-level detection of abnormal working conditions.
- Predictive Modeling Technology: Integrate physical principles with statistical learning to establish industrial knowledge graphs for predicting equipment remaining life and tracing quality defects.
8. Artificial Intelligence
Break through the three technical bottlenecks of algorithm generalization, interpretability, and real-time performance in industrial scenarios.
Small Sample Machine Learning: Develop an algorithm framework based on transfer learning and synthetic data augmentation to address the scarcity of labeled data in industrial scenarios.
Multi-agent Collaborative Decision-making: Build a three-level autonomous optimization system of equipment – production line – factory to achieve distributed intelligent control in dynamic environments.
- Human-Machine Hybrid Enhanced Intelligence: Develop AR-assisted decision-making interfaces and natural language interaction systems to enhance human-machine collaboration efficiency in complex working conditions.
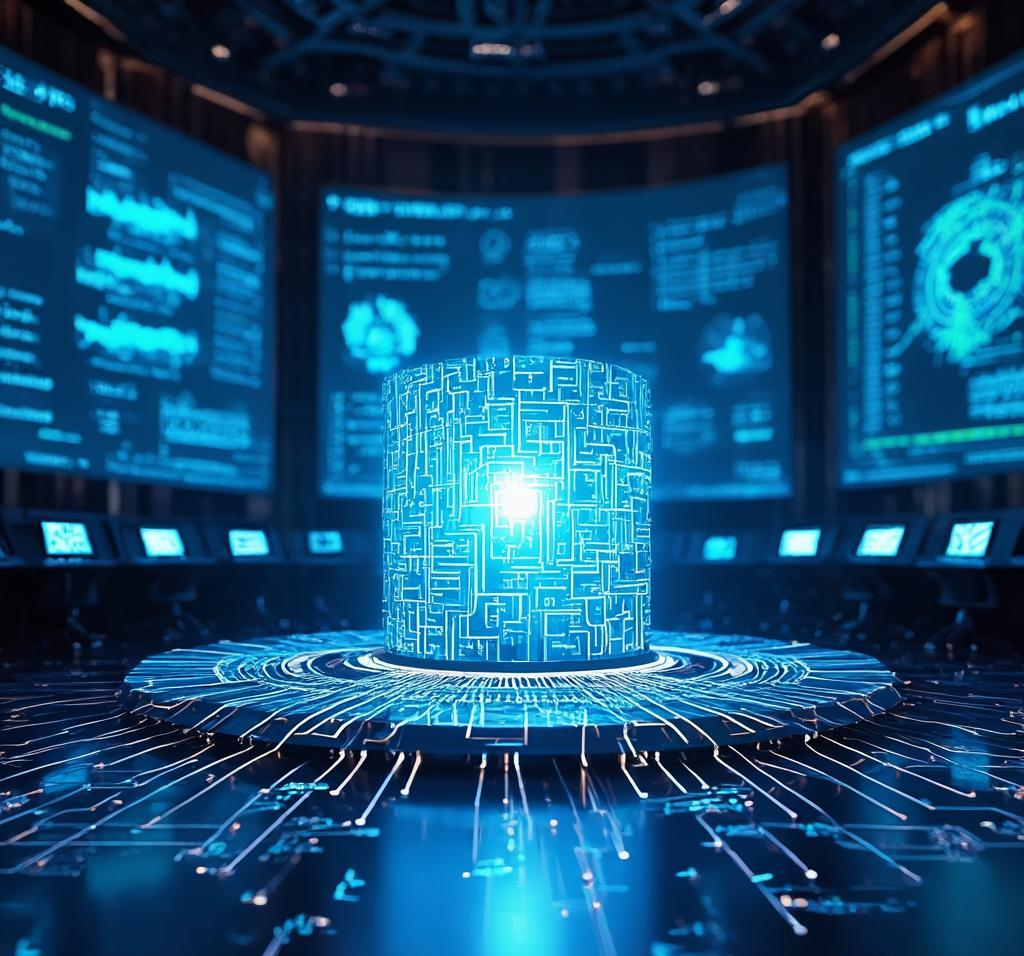
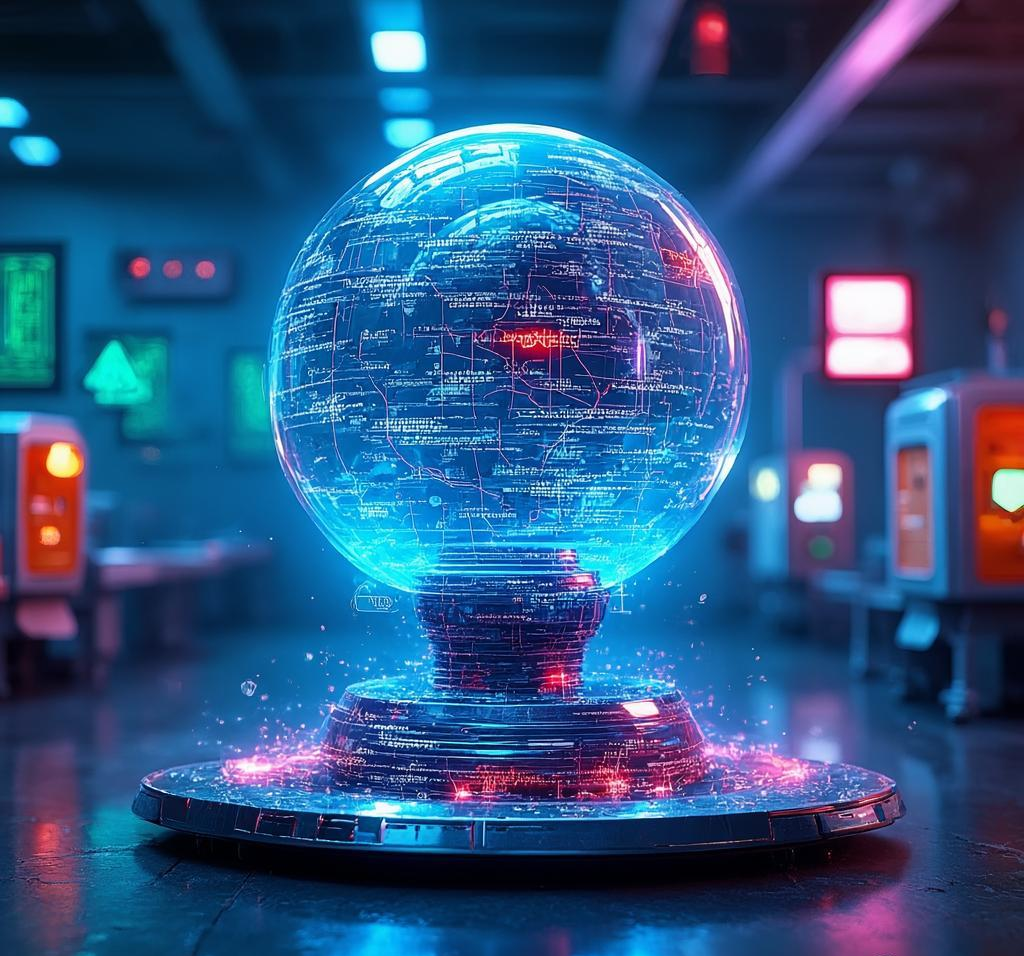
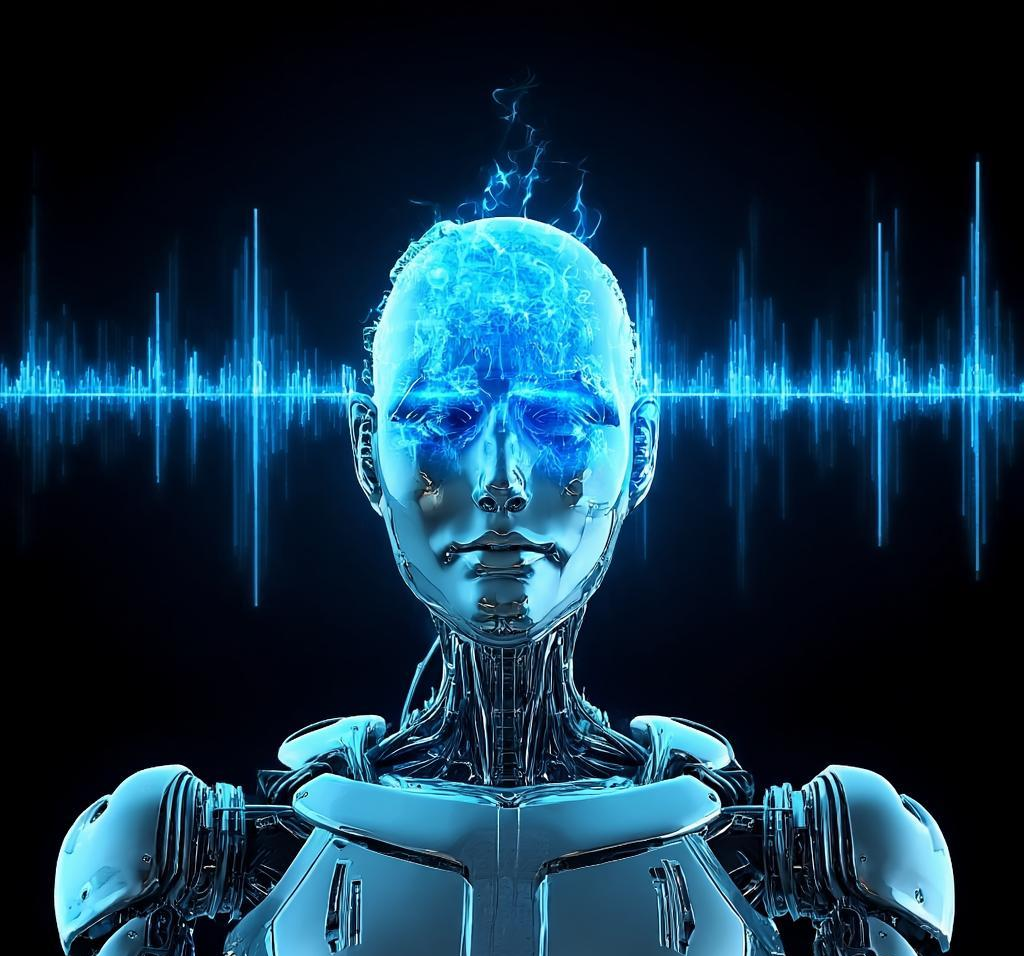